Consumbables for Glass Melting
We have a sub-team with many years of experience in designing and supplying various Electrodes, Electrode Protectors and Throat Protectors for glass furnaces.
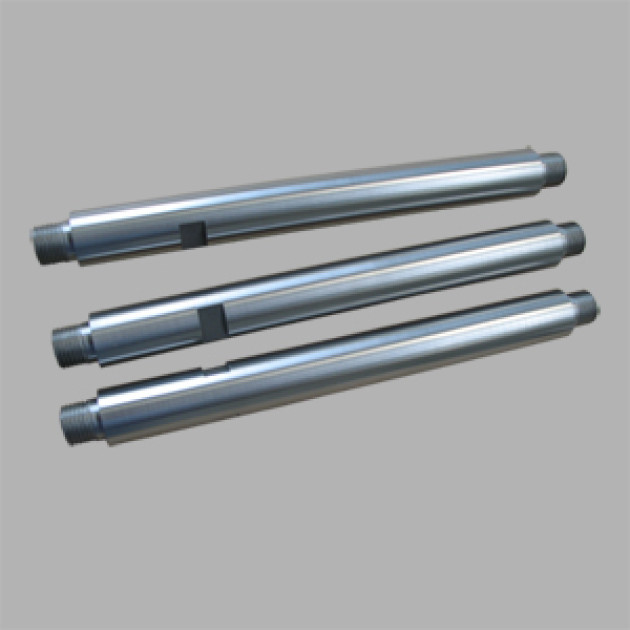
We have a sub-team with many years of experience in designing and supplying various Electrodes, Electrode Protectors and Throat Protectors for glass furnaces.
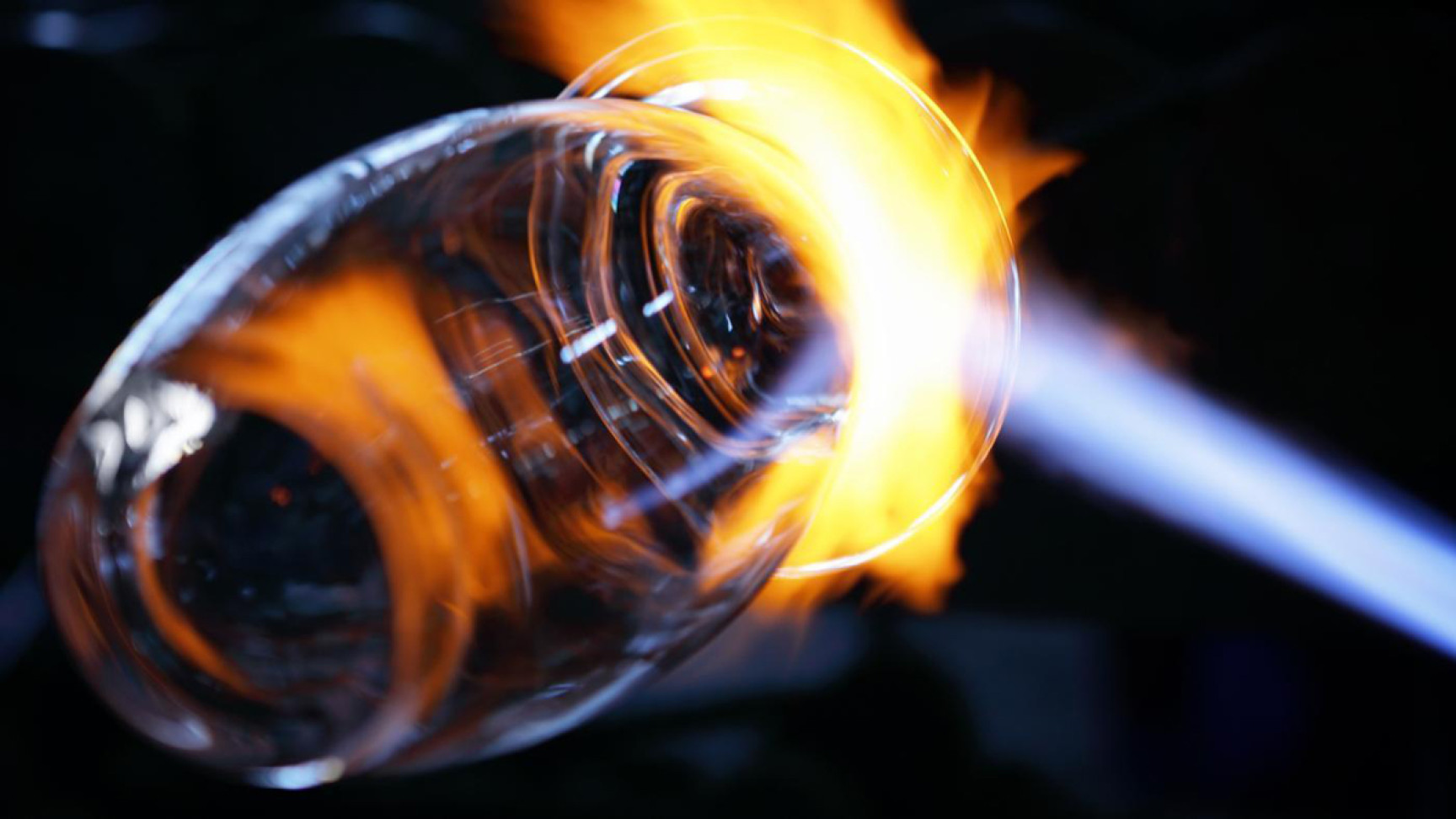
1, Electrodes
a. Mo-La2O3 Electrodes (Through Powder Metallurgy)
The electrodes are made from Molybdenum (Mo) powder (160Mesh/FSSS ≤2.8μm) mixed with 0.2~2% Lanthanum (La). After Molybdenum Oxide (MoO3) is reduced through adding Lanthanum Nitrate (La(NO3)3), La is well distributed on the grain boundary of Mo powder so that Mo crystal’s expansion under high temperatures is restrained thus the Mo electrodes becoming more high-temperature-resistant.
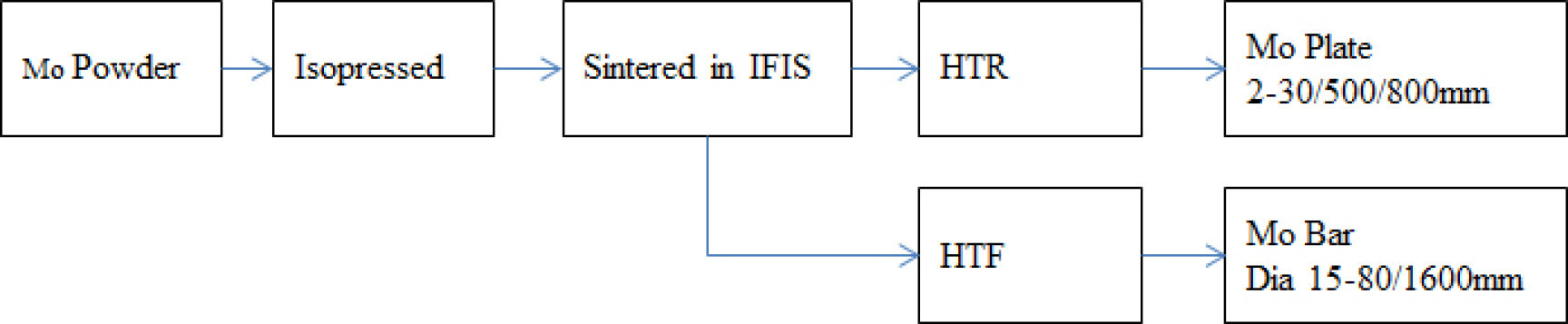
IFSI: Intermediate Frequency Inductive Stove
HTF: High-temperature Forged
HTR: High-temperature Rolled
Specification:
Specimen # | Al (w%) | Bi (w%) | Ca (w%) | Cd (w%) | Cr (w%) |
001 | <0.0001 | <0.0001 | <0.001 | <0.001 | 0.0044 |
Fe (w%) | Mg (w%) | Ni (w%) | P (w%) | Pb (w%) | |
0.0092 | <0.0001 | 0.0058 | <0.001 | <0.0001 | |
Sb (w%) | Si (w%) | Sn (w%) | C (w%) | N (w%) | |
<0.0001 | <0.001 | <0.0001 | 0.0016 | 0.0022 | |
O (w%) | Mo (w%) | / | / | / | |
0.0023 | ≮99.96 | / | / | / |

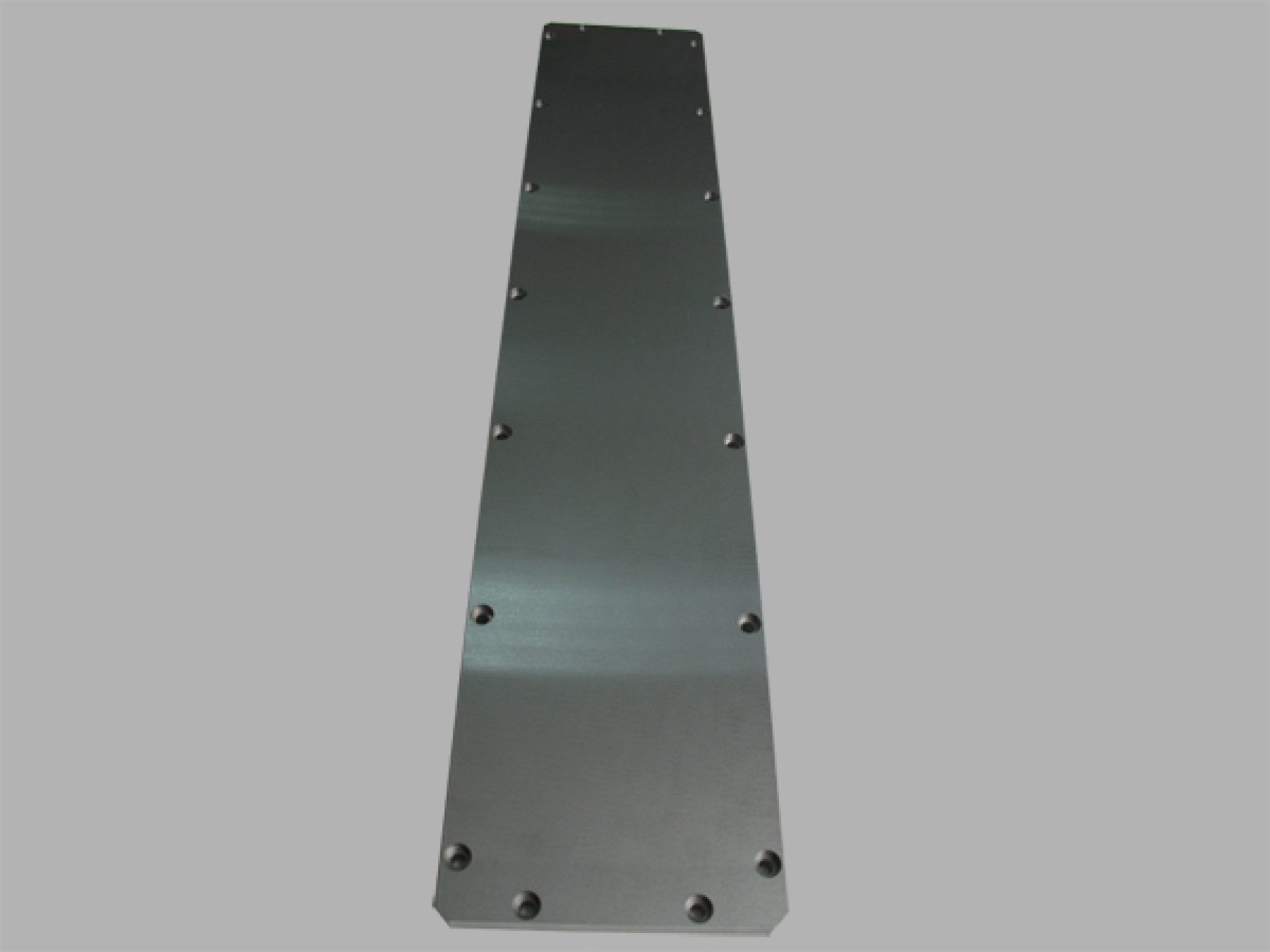
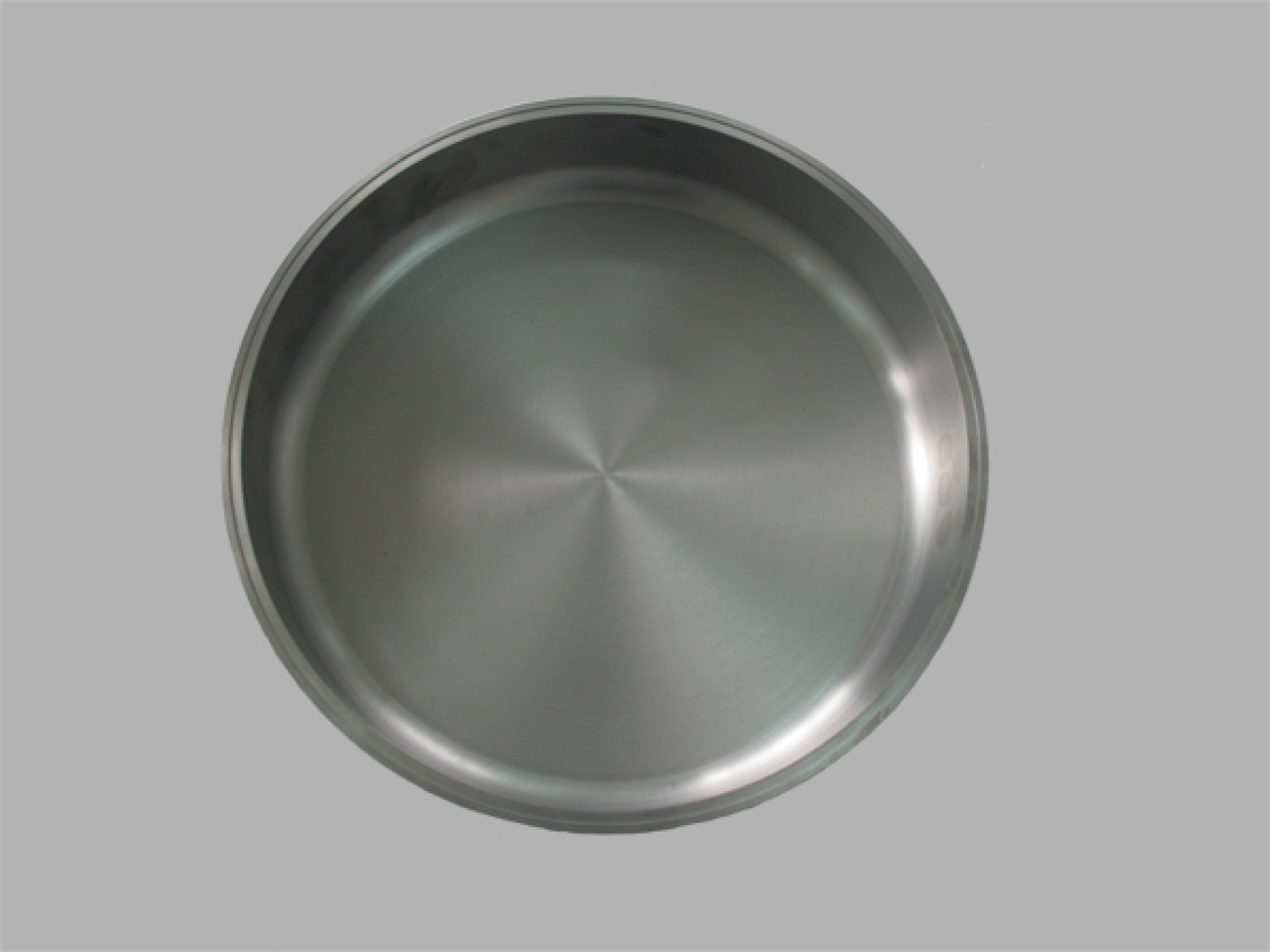
The electrodes are manufactured in a vacuum electron beam furnace (VEBF) at a temperature over 3600℃ and a vacuum as high as 10-2Pa. The high vapour pressure of MoO3 and impurities against the low vapour pressure of Mo prerequisites the mass vapouring of the MoO3 and the impurities thermo-dynamically. Furthermore, how long the vacuum melting lasts decides the extent to which the Mo melts contact with the vacuum, which dynamically paves the basis for the mass vapouring of the MoO3 and impurities. Finally, centre-inclined, compact and coarse bar crystals concrete bottom-up constantly from the bottom of the melting tank. Therefore, vacuum melting does purify Mo, which is capable of achieving theoretical density of 10.2g/cm3 for finished Mo electrodes. Vacuum-melt electrodes are superior to electrodes made by powder metallurgy since the latter, as a sintered solid, bear small crystal grains and big crystal boundaries. When the crystal boundaries reduce in toughness under a high temperature, the Mo electrodes’ service lives fall down. In glass melting, the electrical currency born by a pure Mo electrode triples that by a Mo-La2O3 electrode.

Specimen # | Al (w%) | Bi (w%) | Ca (w%) | Cd (w%) | Cr (w%) |
001 | <0.0001 | <0.0001 | <0.001 | <0.001 | 0.0044 |
Fe (w%) | Mg (w%) | Ni (w%) | P (w%) | Pb (w%) | |
0.0092 | <0.0001 | 0.0058 | <0.001 | <0.0001 | |
Sb (w%) | Si (w%) | Sn (w%) | C (w%) | N (w%) | |
<0.0001 | <0.001 | <0.0001 | 0.0016 | 0.0022 | |
O (w%) | Mo (w%) | / | / | / | |
0.0023 | ≮99.96 | / | / | / |
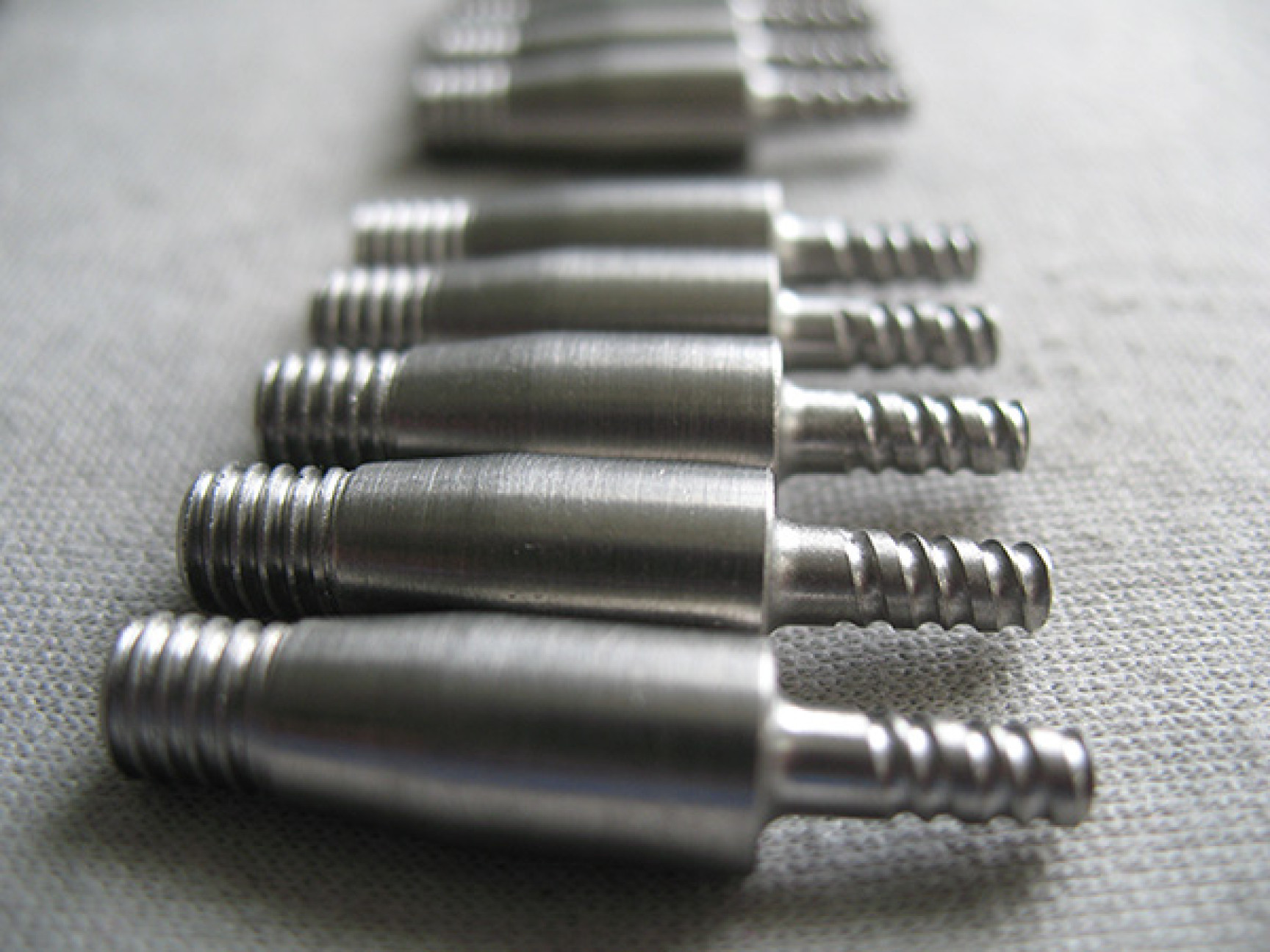
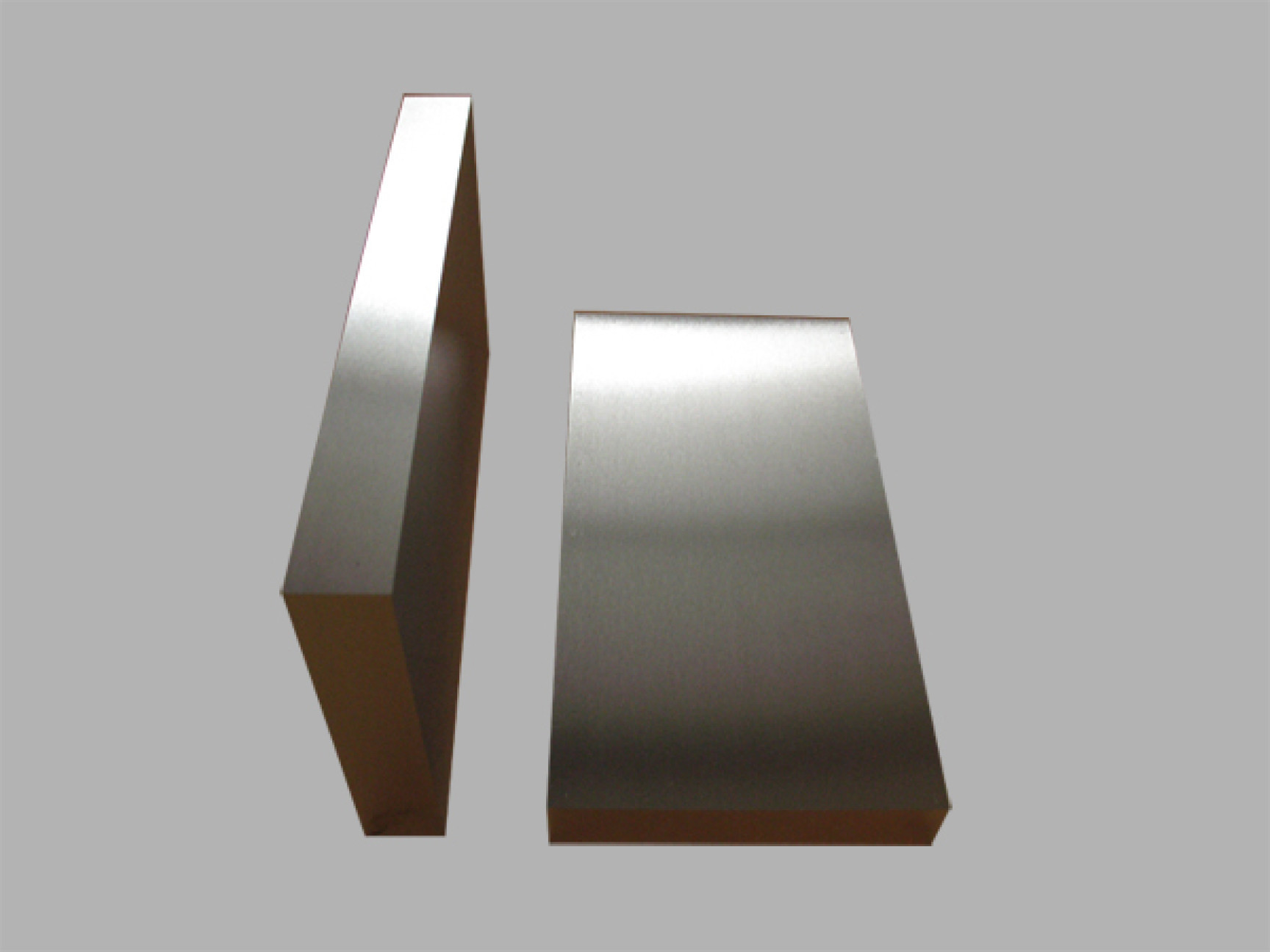
After melted, homogenized and refined in the melting pool, glass liquids flow into a hopper. Through the cooling and adjusting sections of the hopper, the liquids are exposed to homogenous and stable temperature where they shape. Therefore, the performance of the electrodes configured inside the hopper is critical.
Mo is the only material, which is electroconductive while insulating any other substance. No dry cell effect incurs between the glass liquid and the Mo electrodes because nothing else is conductive. Thus, no chemical bubbles form on the surface of the electrodes and in the liquids, which ensures the glass quality.
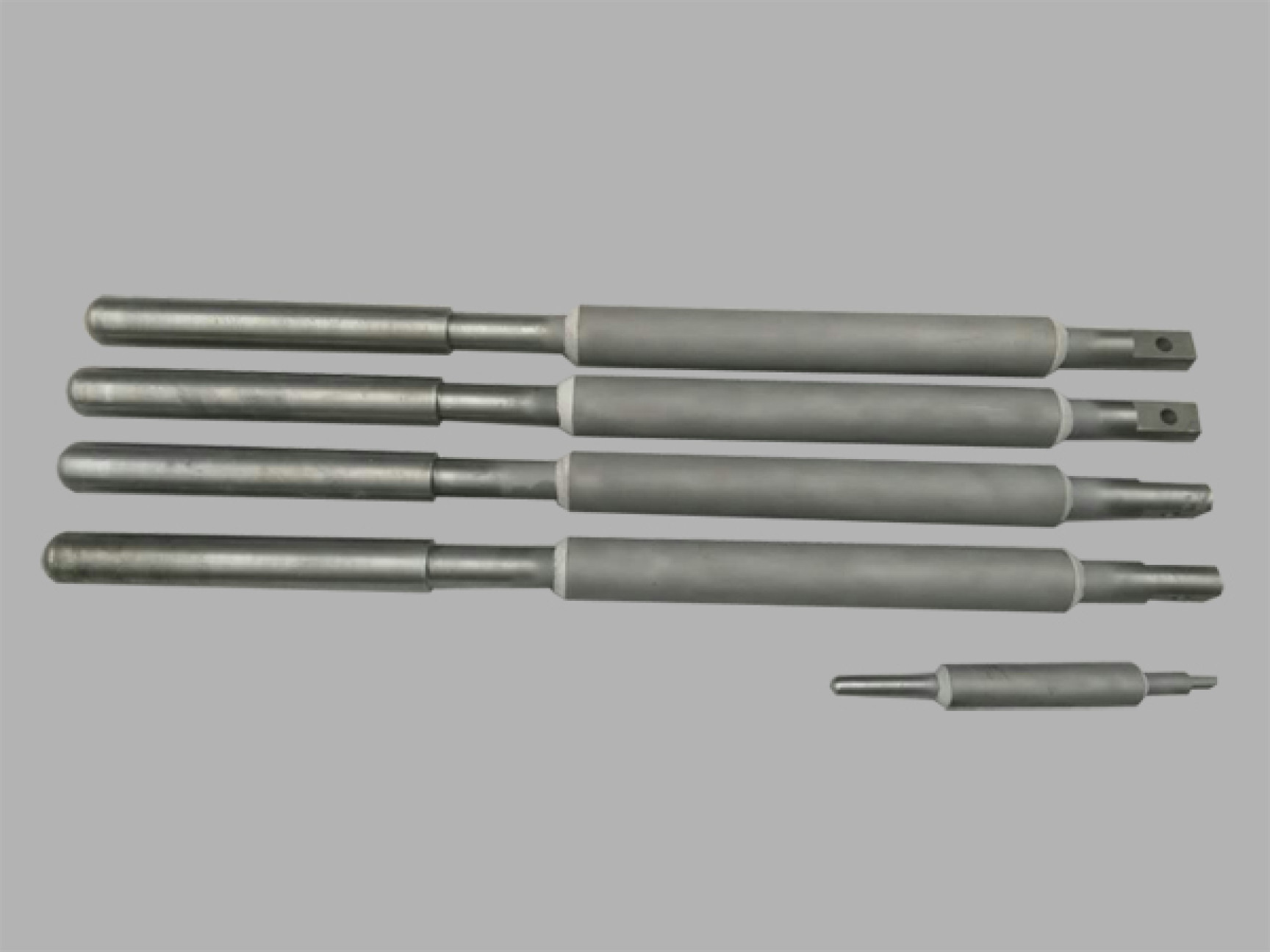
2,Water-cooled Electrode Jackets
a. Ordinary Jackets
The jackets (also referred as water jackets) for electrodes are mainly applied to fix, support and cool the electrodes from oxidizing. We design and manufacture 3 kinds of customized jackets: side, bottom and top plug-in models. With their heads achieved by melting, forging and machining innovative nickel-based high-temperature alloys, our water jackets are capable of resisting excellent high-temperature and thermo-shock and erosion thus ensuring the jackets endure as long as the service life of the furnace. So far, we have designed and supplied turn-key customized water jackets for 500 glass furnaces globally.
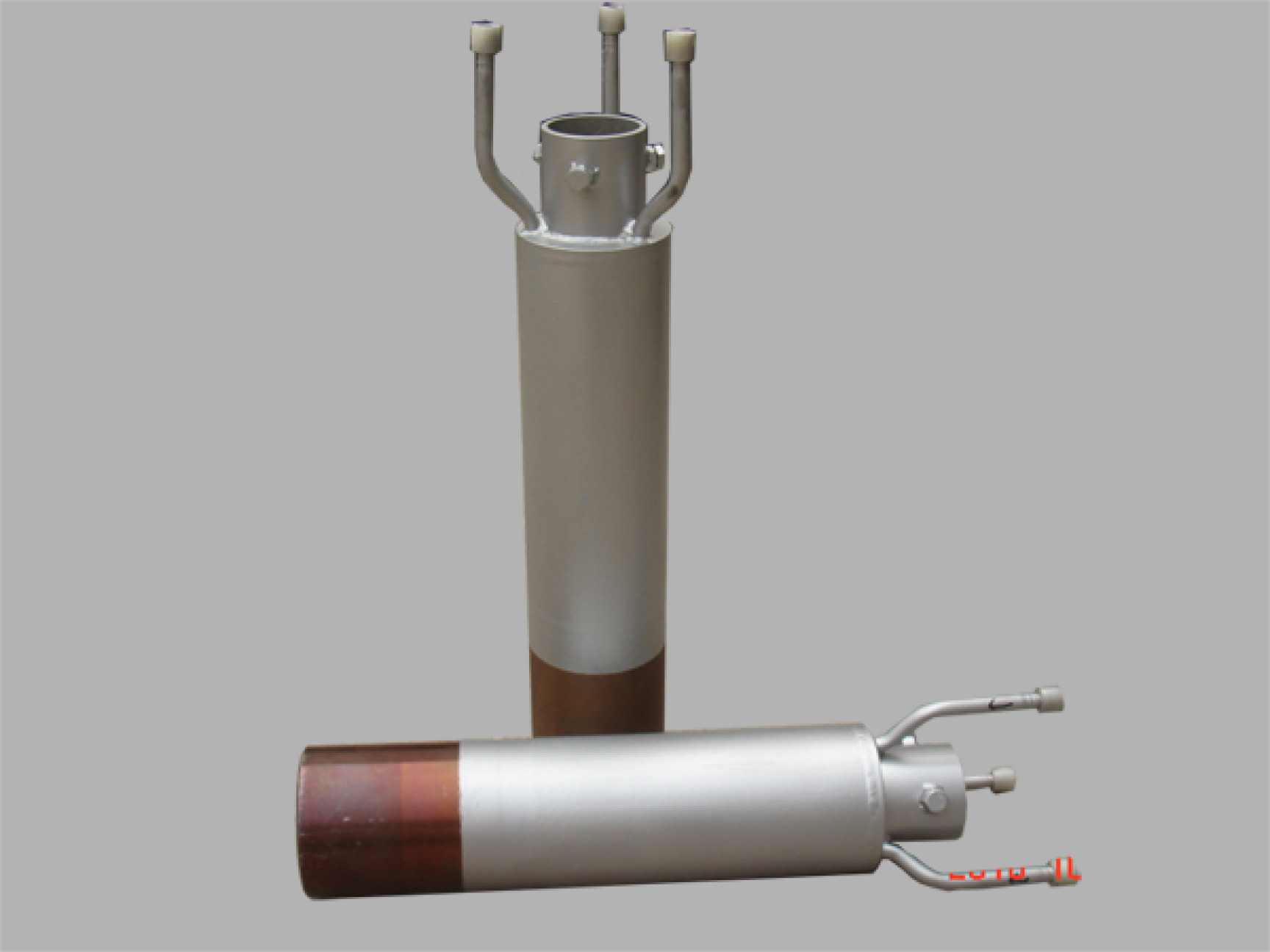
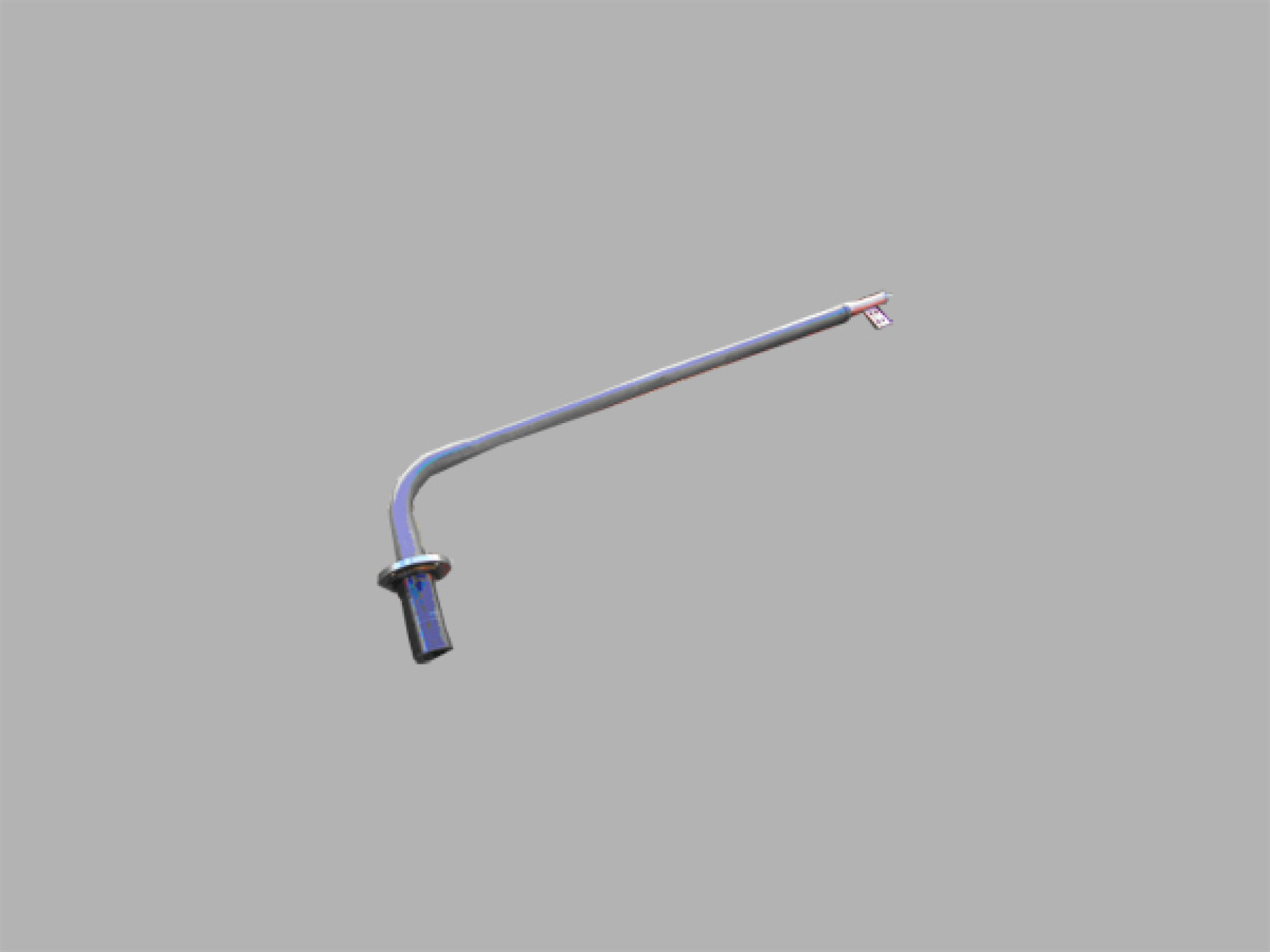
b. Special Jacket
We are proud to have designed a patent-pending Top Plug-in Jacket--a jacket with red copper as the lead body, capable of bearing a 2200A currency. The jacket’s head is delicately protected by ring-shaped Electrocast Zirco-aluminium Bricks (EZBs) from glass melts for 12 months. 12 months later when maintenance incurs, it just takes 10 minutes to replace the Mo half washer and EZBs. That saves all the trouble to separate the jacket from the Mo electrode.
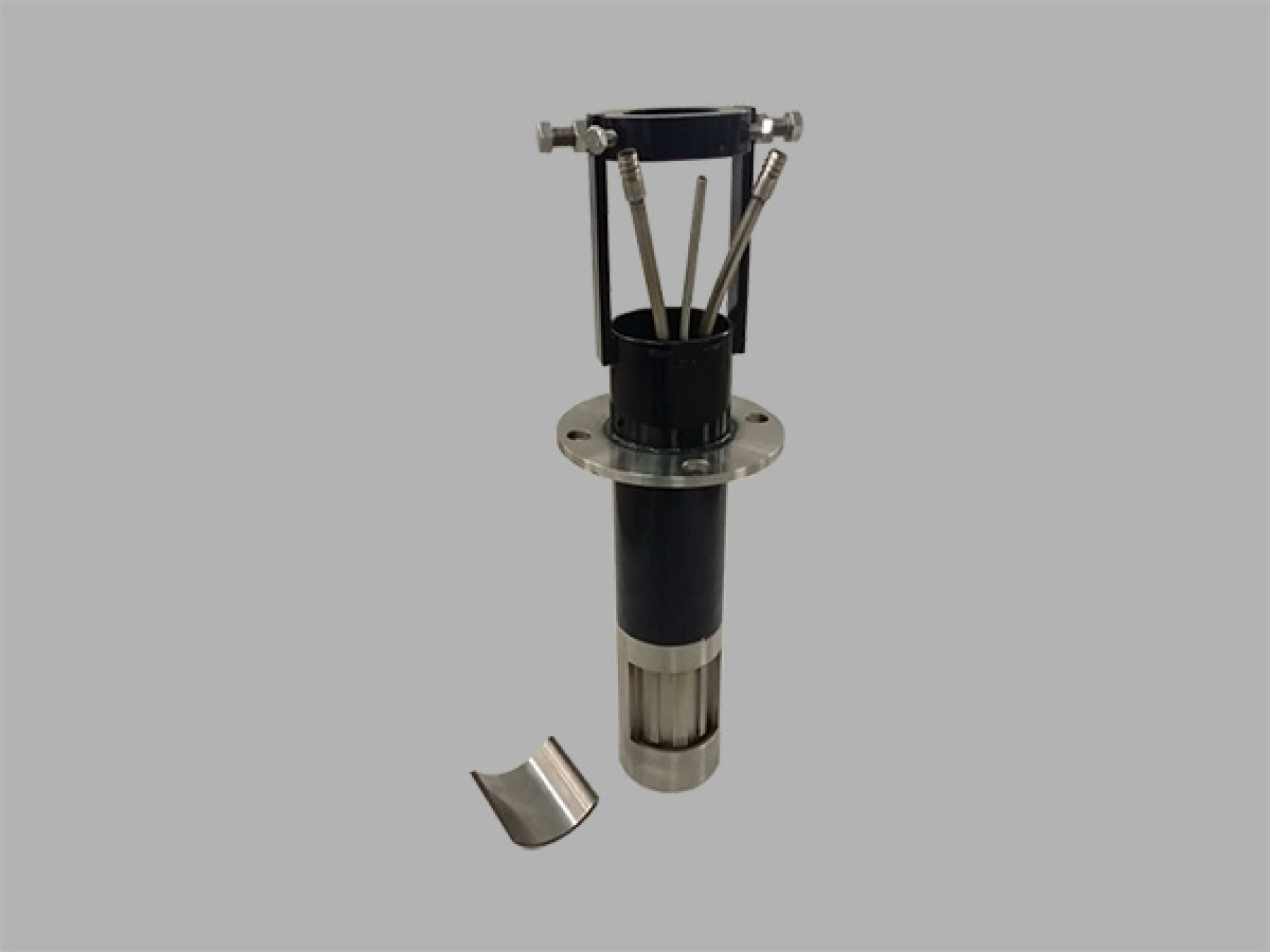
3, Surface-improved Anti-oxidation Mo Protector
Eroded and flushed by glass melts, dog-hole throats and boob bricks are worn out earlier than expected. To longer the service life for the throats and bricks, we have worked out a Surface Improving Technique which refers to deposing an anti-oxidation layer on refractory materials, throat protectors and electrodes. The anti-oxidation materials to be clad on those parts are well chosen to make sure their compositions close to the glass concerned to avoid any spoiling possibility. For the optimal adhesion by the deposed, we apply high-temperature plasma deposing technique.
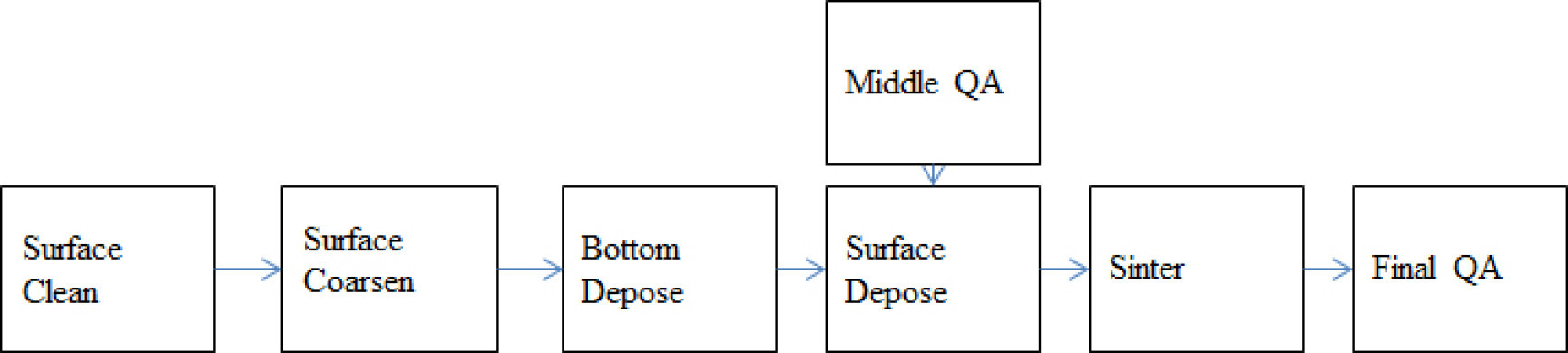
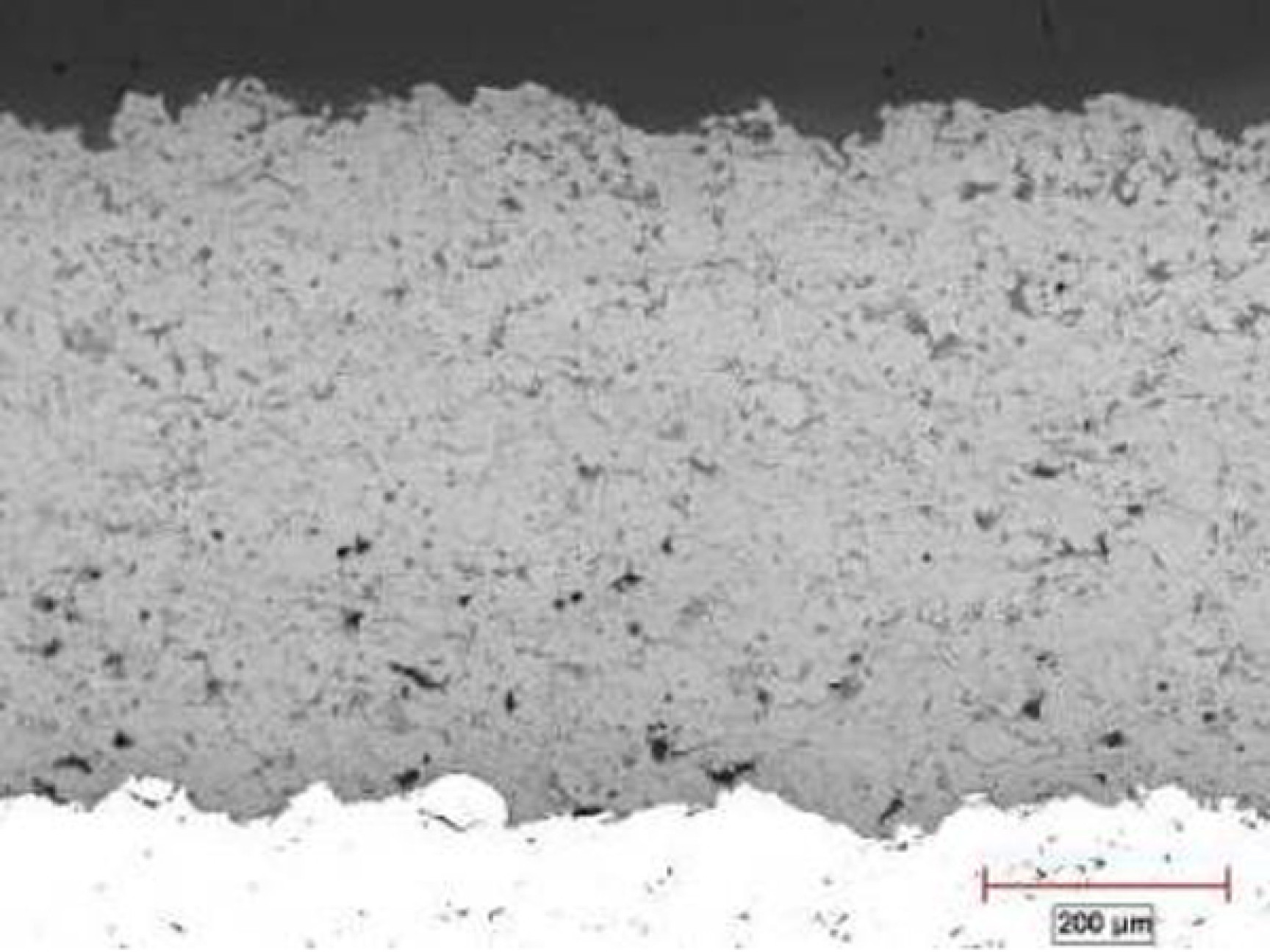
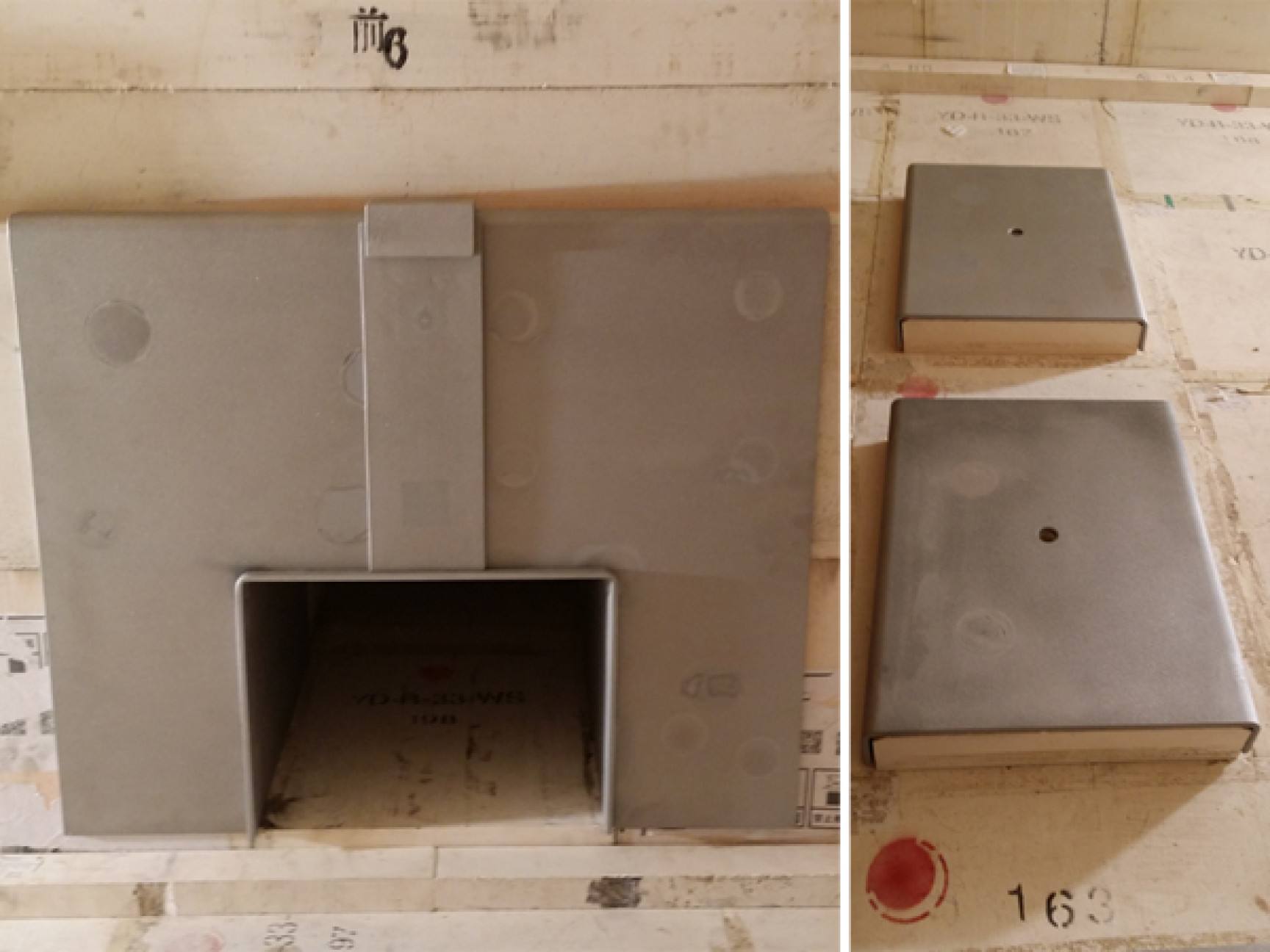
The following graphs show the Aluminum Silicate Cotton (ASC) residue scraped from the peephole on the melting stove after heating up to 1500 ℃ and no Mo volatile was found :
O-K | Al-K | Si-K | Ca-K | Mo-L | |
Base(4)_pt1 | 44.85 | 16.73 | 29.34 | 9.09 | 0.00 |
Base(4)_pt2 | 46.75 | 17.81 | 24.59 | 10.86 | 0.00 |
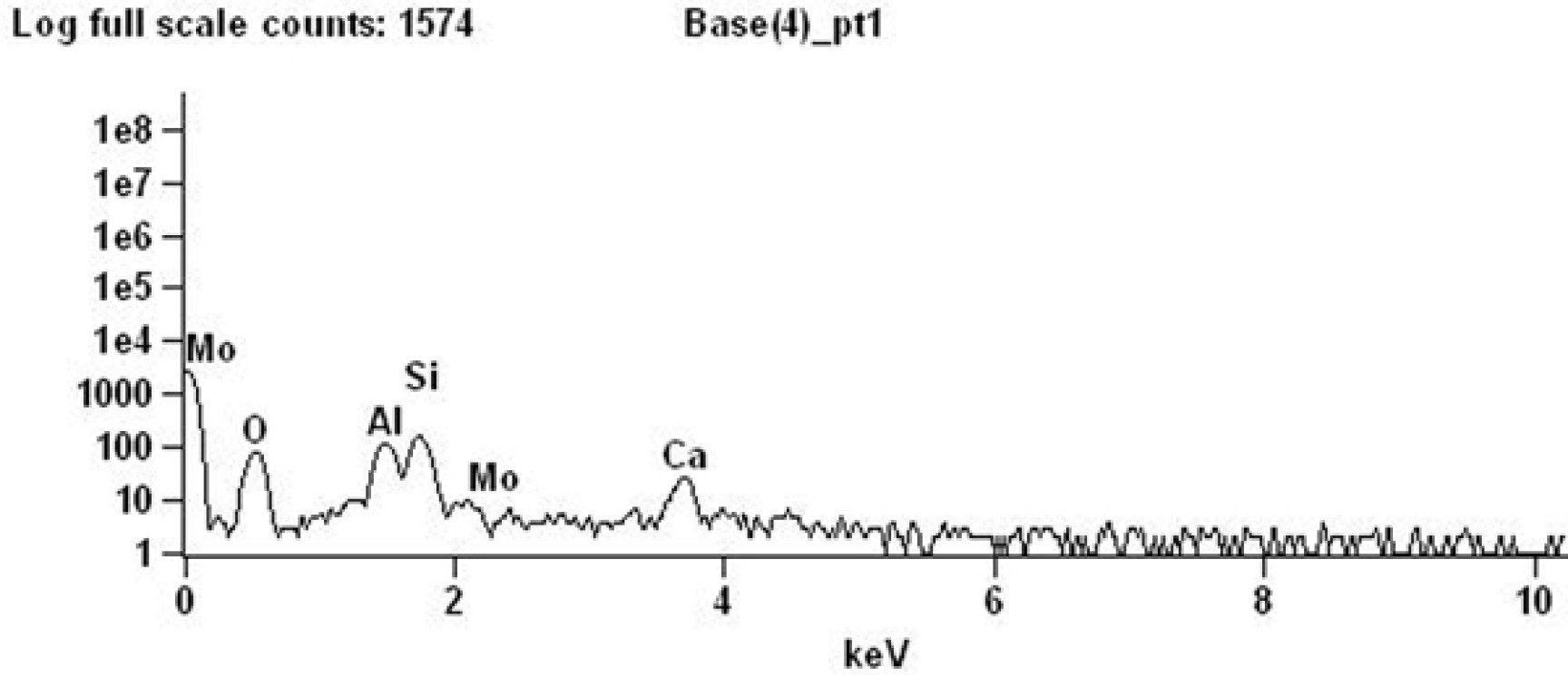
O-K | Al-K | Si-K | Ca-K | Mo-L | |
Base(4)_pt1 | 59.71 | 13.21 | 22.25 | 4.83 | 0.00 |
Base(4)_pt2 | 61.80 | 13.96 | 18.52 | 5.73 | 0.00 |
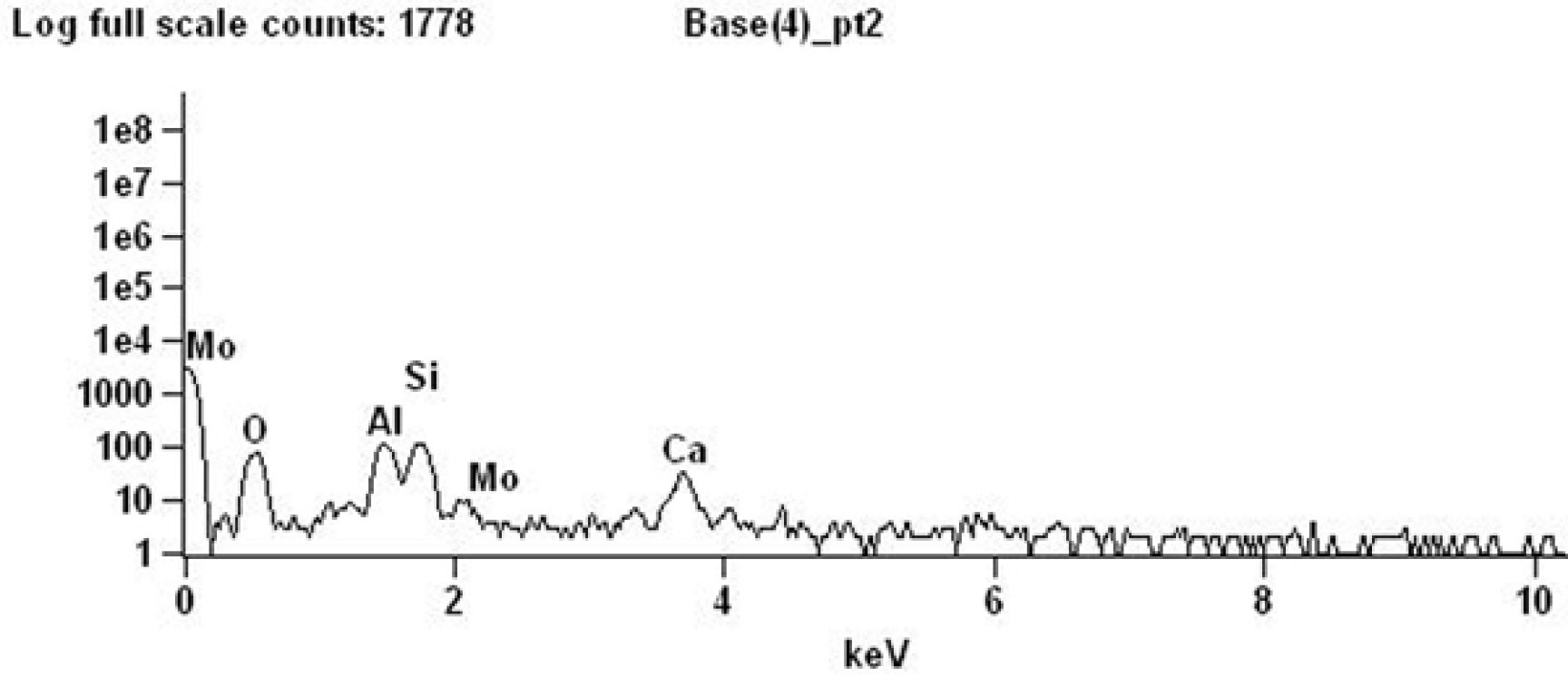
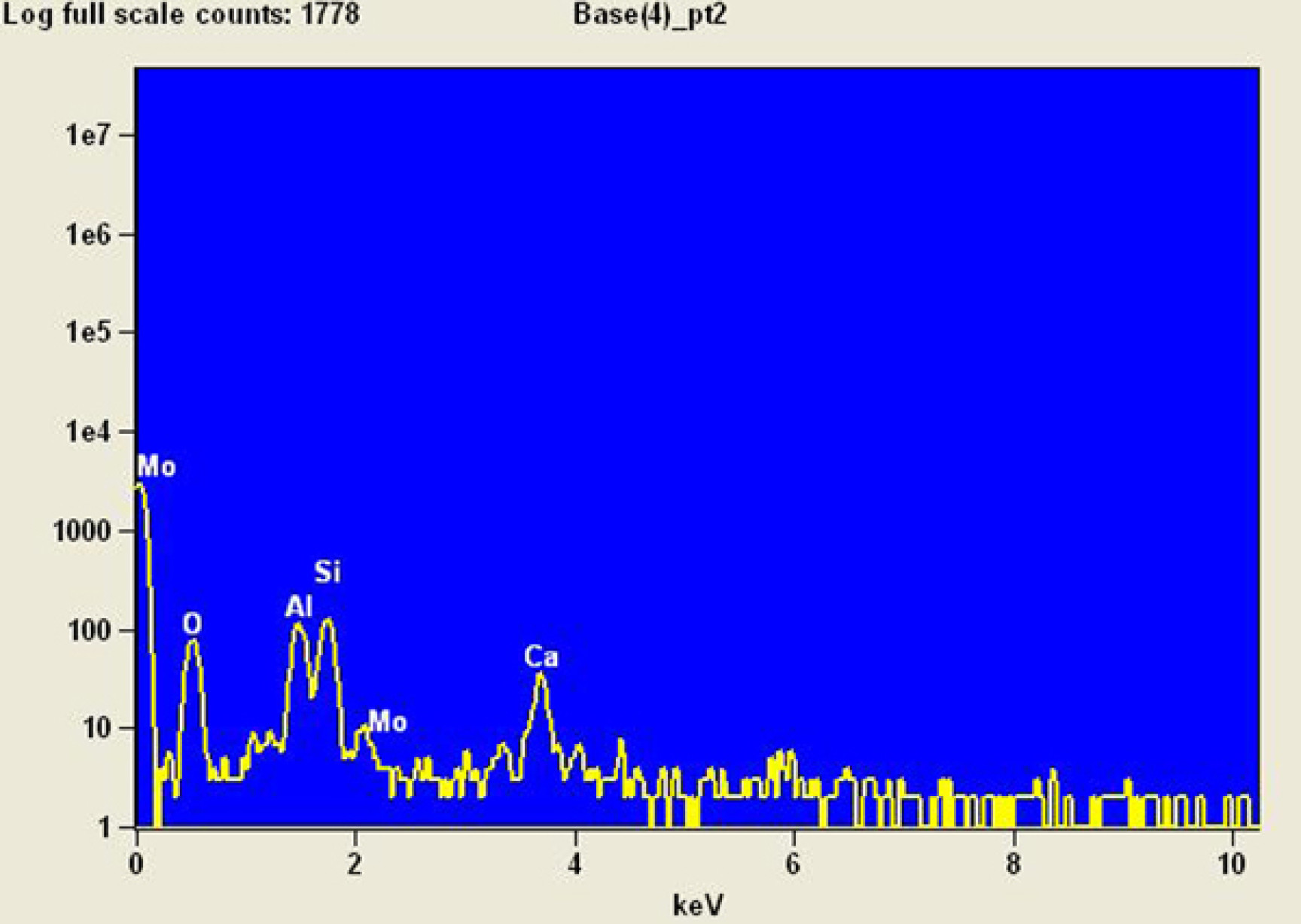