Surface Hardening Technology
Hard-facing refers to a specialist use of depositing metal or ceramics or composite of both onto a mild metal to optimize the superficial wear reistance. This is often done for hard-facing excavating tools, digger bucket teeth and other tools requiring anti-wearable capability.
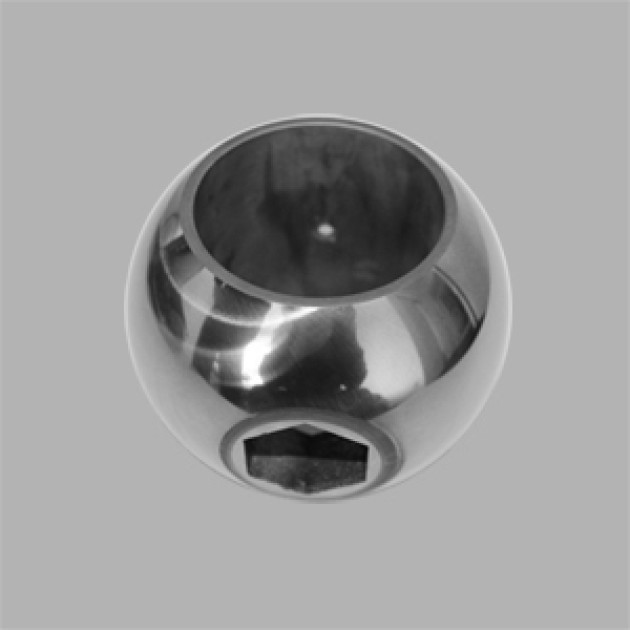
a, Boron Physical Vapour Deposing (B-PVD)
In the process where Boron is deposed on the surface of a ferric substrate, numerous Boron Atoms form, which react with Fe contained in the substrate and compose stable single- or double phase FeB and Fe2B.
#20 Steel 400X
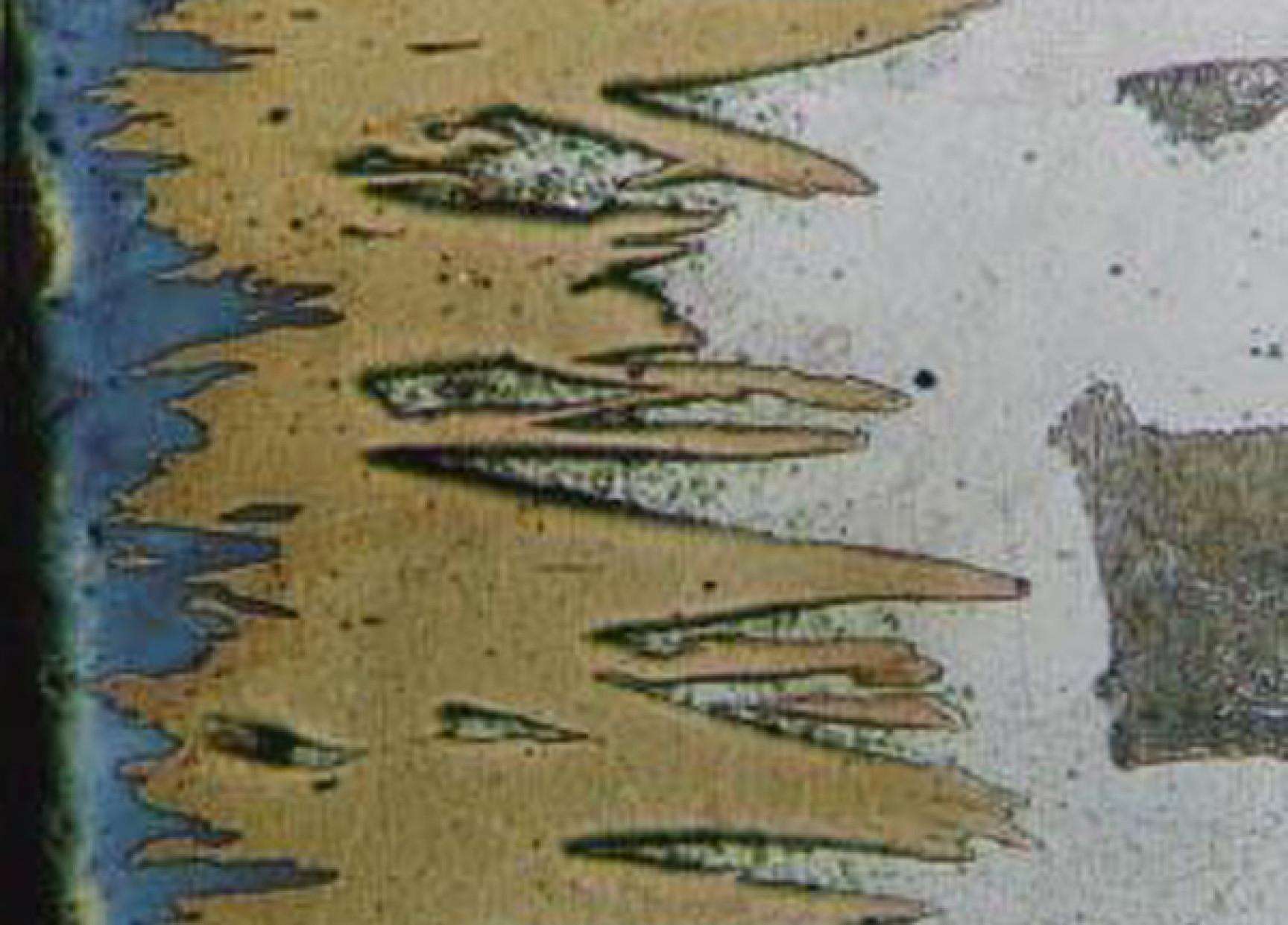
T8 Steel 400X
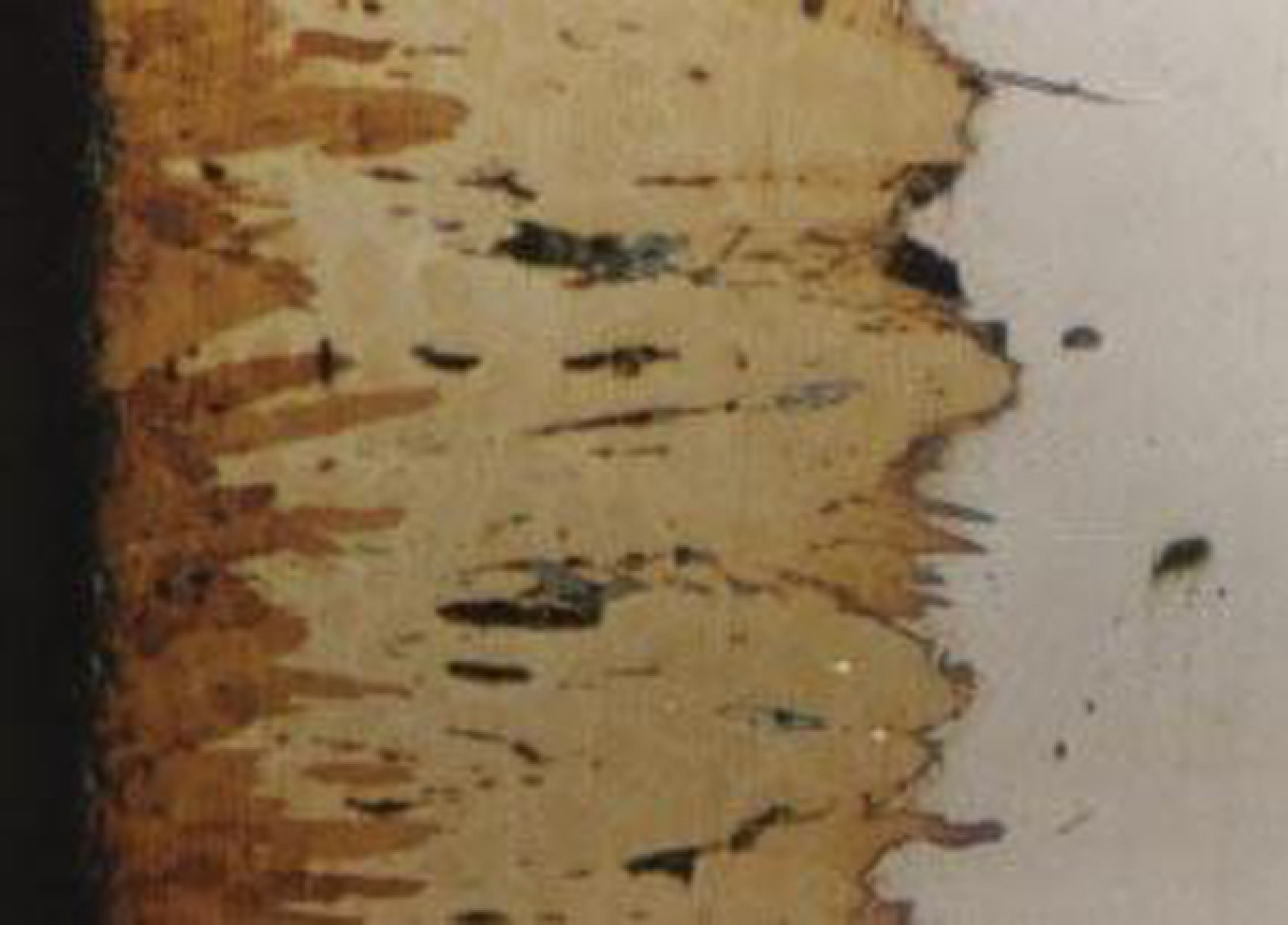
CrWMn 400X
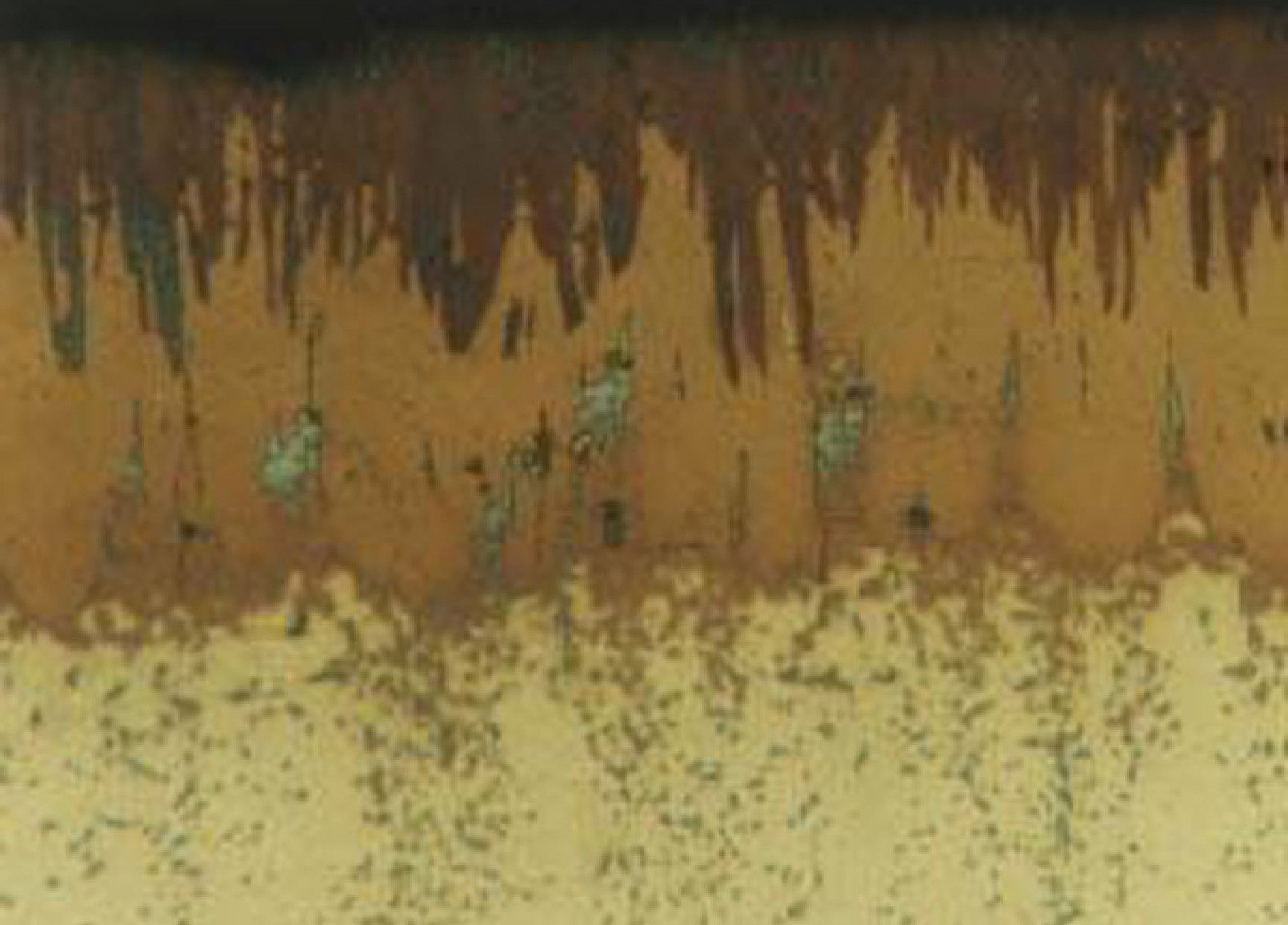
3Cr2W8V 400X
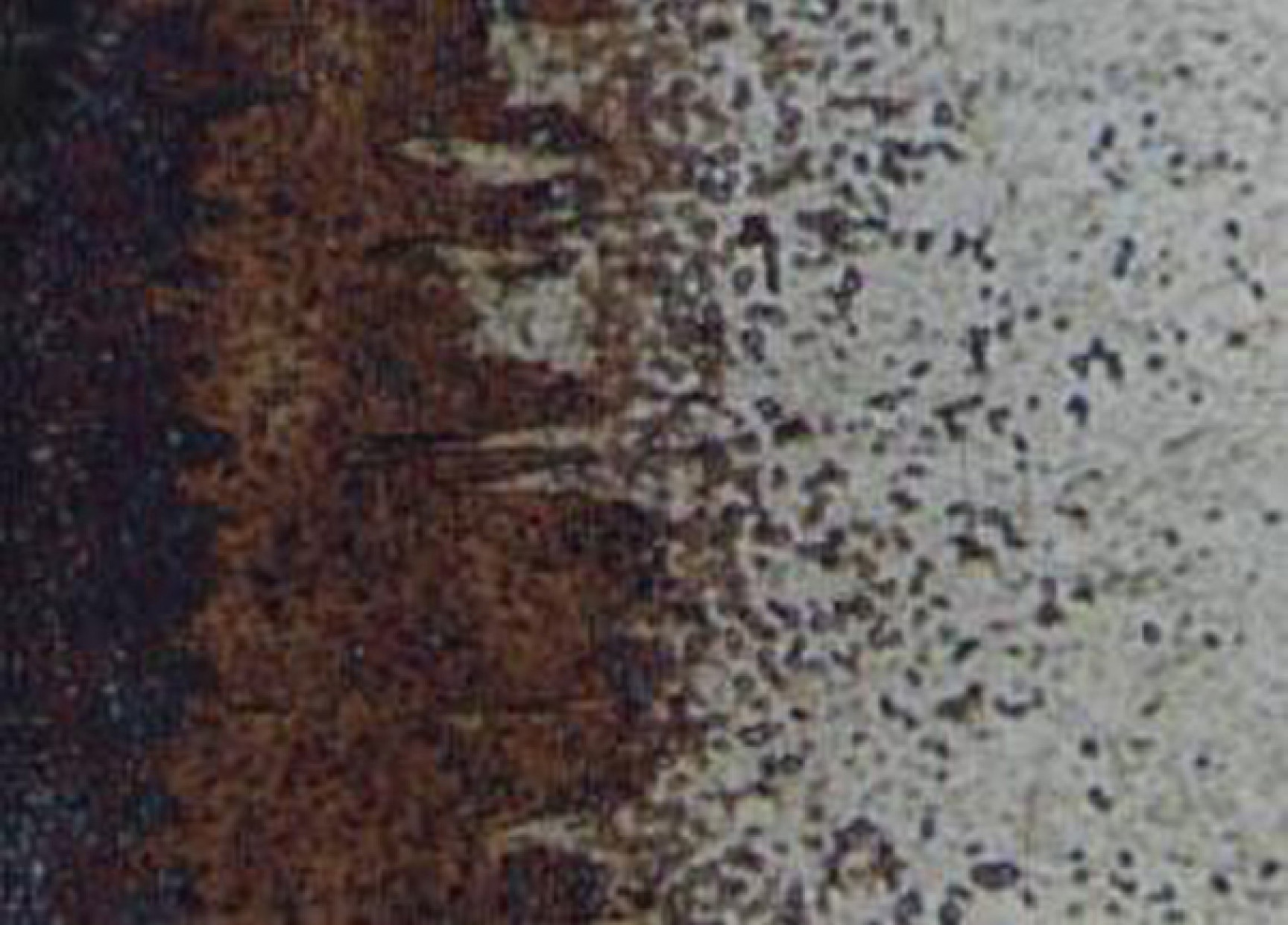
The B-PVD surfaces reach HV 1300~2300 or HRC 73~83 varying on different substrates. After deposing, the durability cold heading and cold drawing dies is fold increased up to tens of times and that of warm-stamping, heading, extruding and forging dies is longered by 3~6 times.
B-PVD’s Charateristics:
The deposing medium is simply composed and environment-friendly.
The deposed surface looks clear and grey, so don’t need washing.
The deposing technique does not require hotcharging, so is easy to be carried out.
The deposing medium can be recycled, so saving costs.
B-PVD’s Applications:
Moulds and Dies
Valve Balls
Valve Rods
Abrasive Blast Nozzles
Other Wear and Erosion-resistant Parts
b, Metallic Ceramic Coating (MCC)
The coating mainly carried out by flame-spraying ultrasonically is characteristic of high-speed particle, fine and homogenous coverage and excellent adhesion on the coated object. Since it contains ceramic grains bonded by metals, the coating achieved is able to tolerate wearing and flushing by fluids
Index Value
Thickness 0.1~0.3mm
Hardness HV0.3~1200 or HRC~75 for WC12Co and WC10Co4Cr
Adhesion 60~80 MPa
Porosity <1%
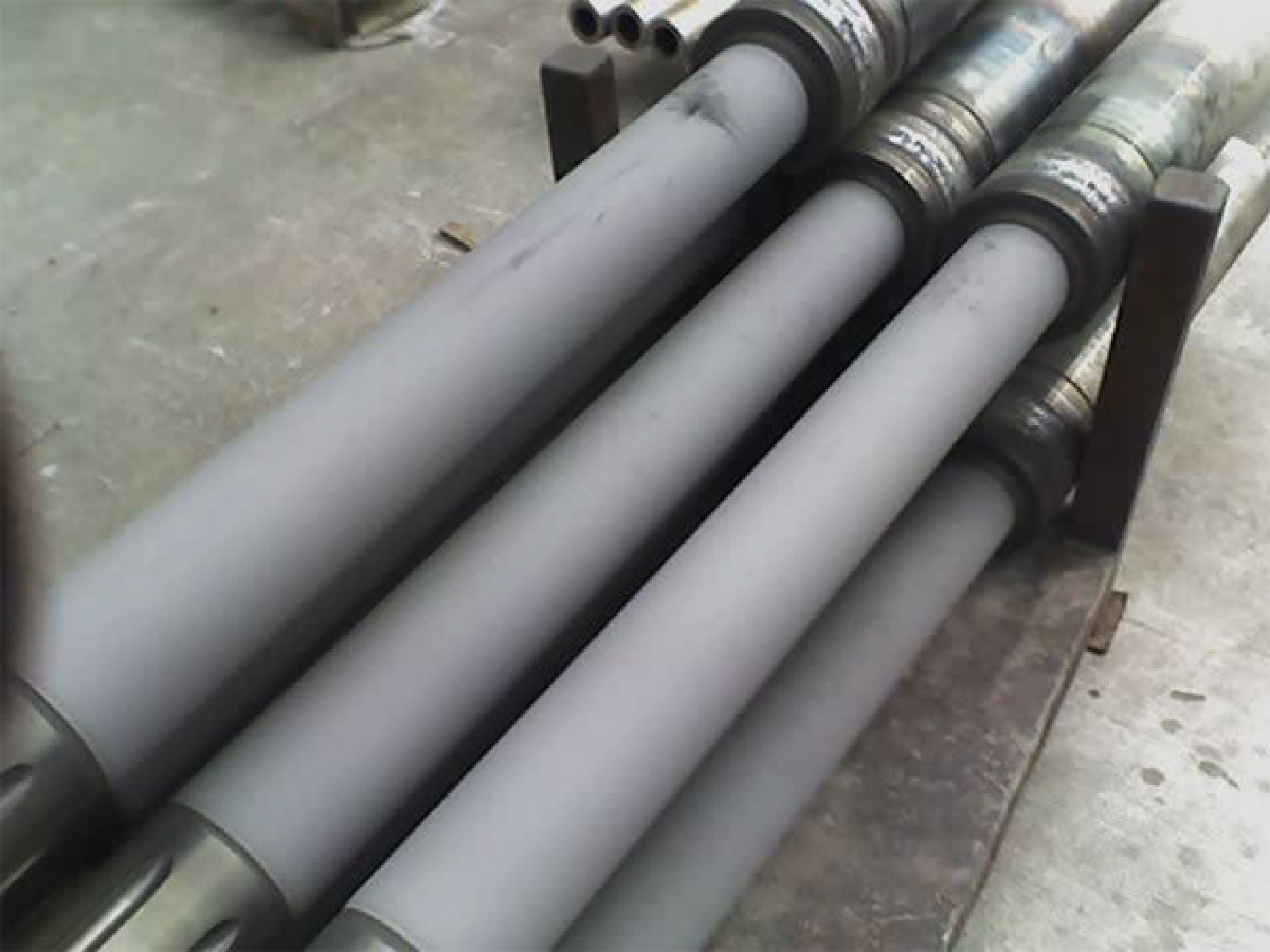
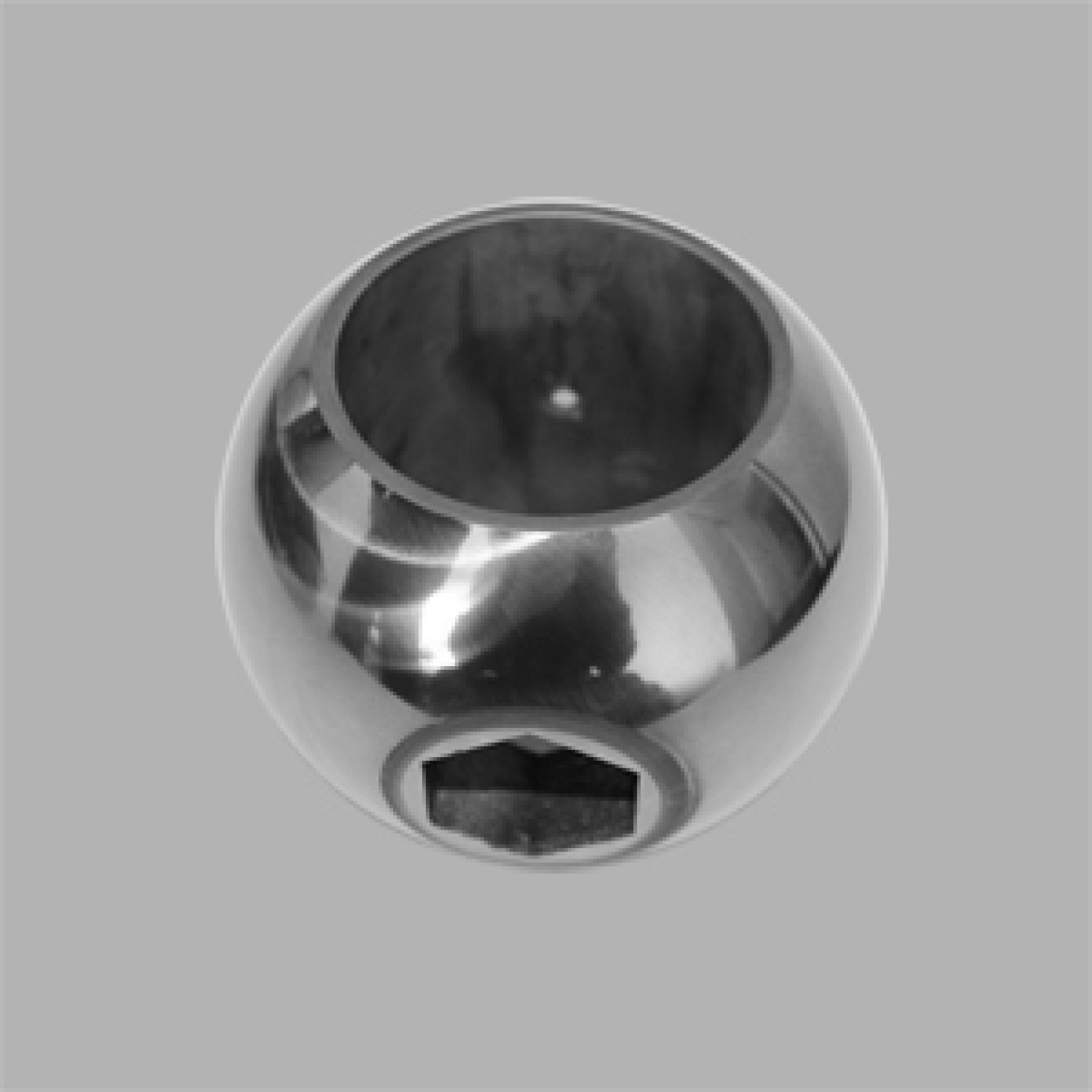

c, Laser-cladding Coating (LCC)
The techniques which provide well adhesive and thicker coatings is mainly used in dimension offsetting and carrying out wearable coatings like nickel alloy, cobalt alloy and magnet-free coating under such sever condition as down hole.
Index Value
Thickness 0.5~3mm
Hardness HRC 20~60 ; 3-5 times more anti-wearable than normal alloys
Adhesion 300 MPa
Porosity Porosity-free
It is proven at an oil well in North China that the service life of a drill collar with a laser-cladding coating serve is 3-5 times longer than a drill collar without the same coating. Moreover, the drill collar can be renovated after the coating drops off to save costs.
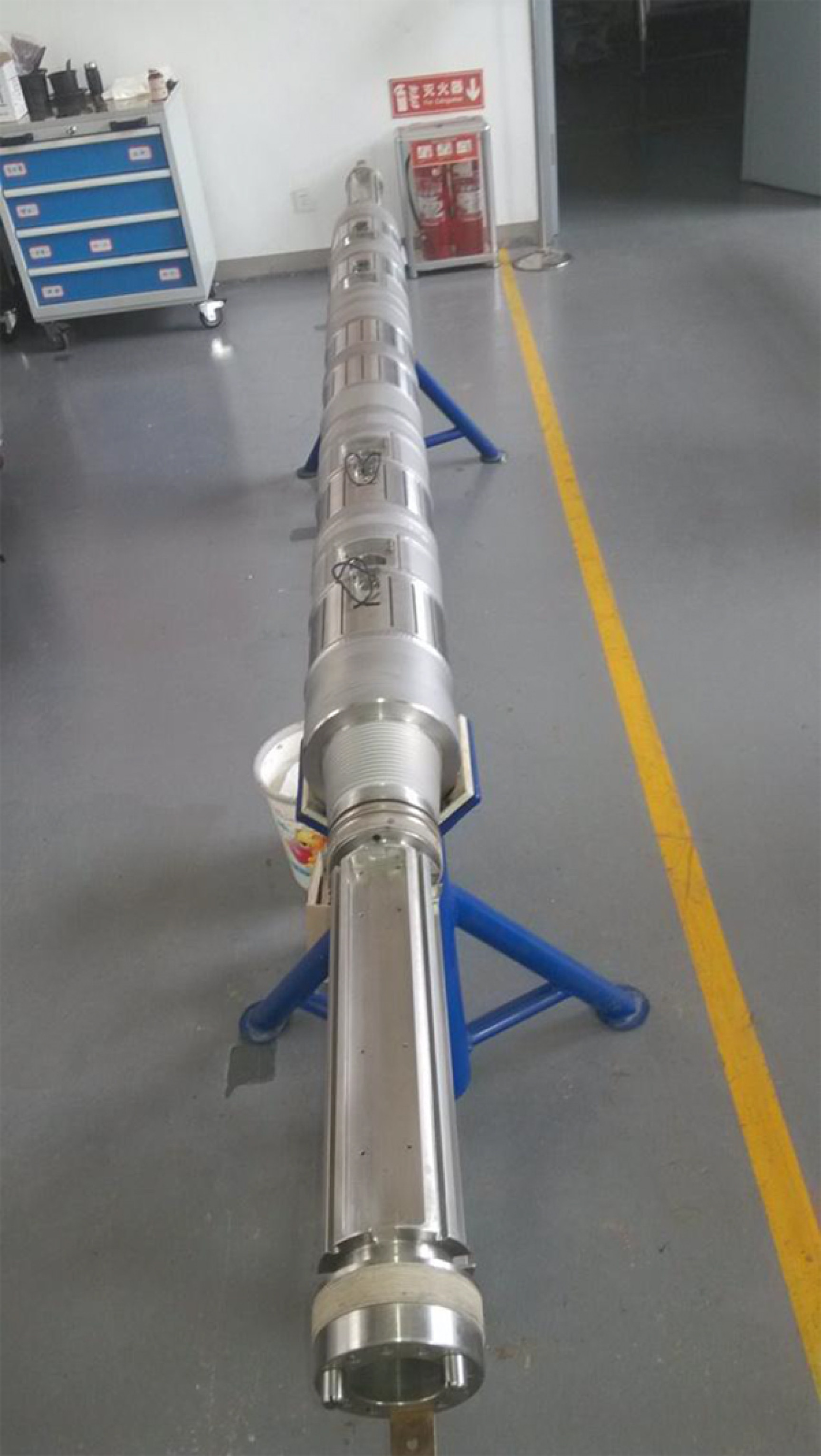
d, Ceramic Insulating Coating (CIC)
The technique is mainly used in insulating exploration and production (EP) systems. The ceramic insulator coated on both sides of the port well live with big torque.
Index Value
Thickness 0.1~0.3mm
Adhesion 30~40 MPa
Porosity 3-5%
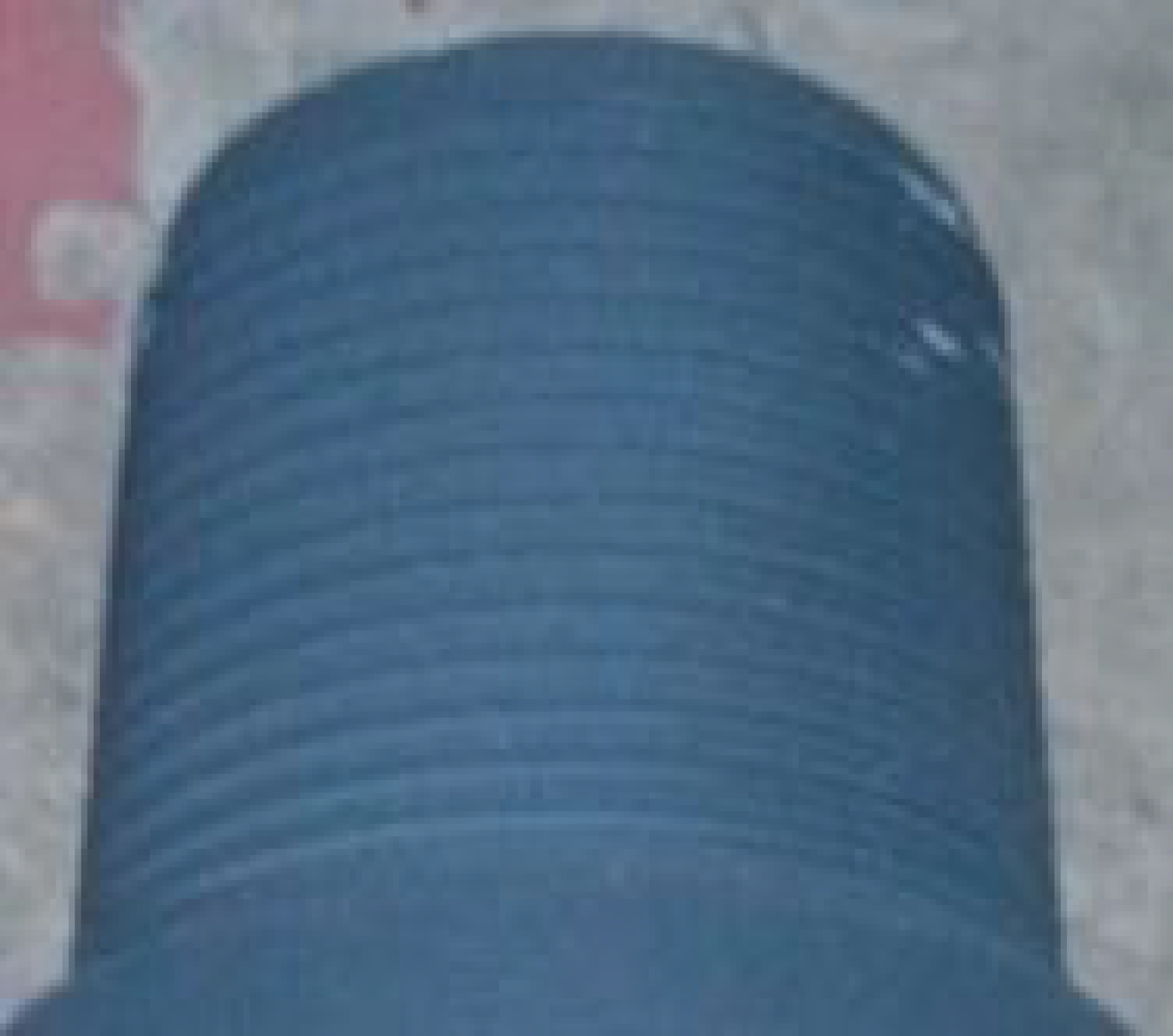